Falls from height remain the biggest cause of death in the workplace, with 67 recorded in Great Britain in 2003/04. It is believed that many of these deaths could have been avoided if sensible measures had been taken. In addition, nearly 4000 people suffered a serious injury as a result of a fall from height in the workplace during the same period.
In line with its policy of openness, the HSE (Health and Safety Executive) has published the information that it uses to train HSE and Local Authority Inspectors in enforcing the Work at Height Regulations 2005 (WAHR) that came into force on 6 April 2005. This material, together with the guidance already available, will help people better understand their obligations under the WAHR and what constitutes safe working at height.
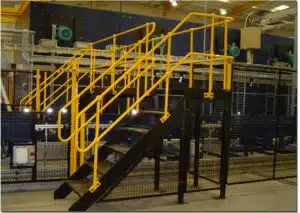
HSE publishes its own Work at Height training information
Dr Elizabeth Gibby, director of the HSE’s Injuries Reduction Programme, said: “The publication of this pack will help health and safety professionals to understand more about the HSE approach to the Work at Height Regulations. It is an important step forward in openness from HSE. It is sensible to share information to help people to be safe at work“.
The pack gives employers, safety professionals and those who work at height an opportunity to look at the information provided to inspectors and it shows examples of the type of good and bad practice that inspectors look for during their visits.
“Not guidance”
Nonetheless, the Pack is not ‘guidance’; it merely gives access to the same information that HSE Inspectors and Environmental Health Officers use when performing their regulatory duties.
The Work at Height Regulations set out a simple hierarchy for managing and selecting work equipment for work at height. Duty holders must: avoid work at height where they can; use work equipment or other measures to prevent falls where they cannot avoid work at height; and where they cannot eliminate the risk of a fall, use work equipment or other measures to minimise the distance and consequences of a fall should one occur.
As with any other activity with safety implications, the first step to take is to perform a risk assessment. An important point raised in the Training Pack is the significant difference made by having an ‘existing safe place of work’ – which would be identified in a risk assessment. If none is available, considerable work must be undertaken to select and implement the most appropriate measures to avoid a fall, prevent a fall or mitigate the effects of a fall. Furthermore, there must be an inspection of the measures before the work at height commences, and this must all be documented.
On the other hand, if a safe place of work already exists, there is simply a requirement for a visual inspection by a competent person – with no need to record the findings.
So what constitutes an ‘existing safe place of work’? This might be access platforms, guard rails, fixed ladders, stairways or similar permanent structures. And the cost of these is not as great as might be expected.
Permanent access can be more cost-effective
Procter Machine Guarding suggests that, in general, permanent access is more cost-effective than traditional or tower scaffolding after it has been used as little as three times, though the need for additional management time to conform fully with the new WAHR makes permanent access platforms even more viable.
If suitable platforms, walkways and fixed ladders are in place, no time is needed to assemble the means of access, and the labour requirement is often reduced from two or more down to one. There is also no disruption to production caused by scaffolding obstructing access at floor level, and companies that have installed access platforms often find that easier access means that maintenance takes place more frequently or at more convenient times – leading to higher quality production with more consistent output. Another benefit is that bespoke access platforms usually provide better access than tower scaffolding because they can reach over and around plant, and, in the case of emergency maintenance following an unplanned stoppage, access is gained immediately and downtime is minimised.
Aside from improving safety and reducing the cost of maintenance, custom-designed access platforms can also provide the optimum location from which to control processes, view production or replenish hoppers of raw materials.
The Procter Machine Guarding service
Procter Machine Guarding has over 50 years of experience of supplying bespoke access platforms. Customers are offered a free site survey, after which a quotation is prepared that includes the costs of designing, manufacturing and installing the platforms, ladders, guard rails and associated hardware to the customer’s specification. All designs are completed in accordance with the requirements of the EEMUA (Engineering Equipment and Material Users’ Association) as well as relevant British and European standards.
Designs are done on site, which ensures they take full account of control panels, cable ducts and similar obstructions, and are highly accurate – which also helps the installation to be completed as quickly as possible. Installations can be scheduled to take place at weekends or during planned maintenance shutdowns so as to avoid disruption to production. Procter Machine Guarding has its own teams of experienced fitters that can travel anywhere in the UK and Ireland.
The HSE has published a Falls from Height document that is intended for use by its inspectors. In addition, the HSE offers a freely downloadable guide to Working at Height (INDG401) and several other publications relating to Working at Height, plus there is more information in the Work at Height section of the HSE Website.
To discuss any requirements for access platforms, please contact Procter Machine Safety